This project consisted of a 100,000 square foot renovation and a 200,000 square foot new addition to a food processing facility. This included over 18 miles of total piping, 12 of which were prefabricated in our shops.
The prefabrication included 106 Utility Pipe Racks up to 40’ in length, suspended from structure, 40 Refrigeration Racks up to 54’ in length, and Control Valve Groups for over 125 pieces of equipment.
Key Project Elements:
- 100% Revit Prefabrication
- Coordination
- Piping Bar-Coding
- Total Station Hanger and System layout
- Piping Weld Mapping and Tracking
- Multi Locational Prefabrication – On Time Delivery
- Duct: Supply, Return, Exhaust, Welded Stainless Steel Exhaust, VAV, RTU, MAU, GIV, EA FANS
- Helicopter Equipment Sets
- Mechanical Refrigeration Piping: HHW, CHW, Glycol, Ammonia, Hot Gas, Condenser water, Oil Cooling, Condensate
- Utility Piping Services: Steam, NG, CA, Floor Foamer Chemical, Disinfectant Chemical, Sanitizer Chemical, Domestic Waters, High Pressure Hot water, Softened water, Tower Water, Condensate
- Piping Flat Racks
- Piping Multi Level Racks – Flat and Sloping
- Exterior Piping & Racks
- 75+ AHUs, 18 RMAUs, 6 Refrigeration Compressors and Condensers, Sump tanks and pumps, Fluid coolers and Specialty Pump Skids, Underfloor Warming Skids, Diffusion Tanks, Compressor Skids
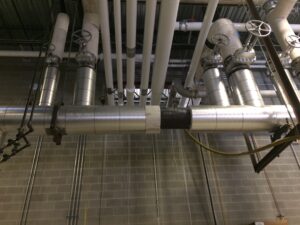
This project consists of a new 2-story, 78,000 square foot Cancer Center. This includes a dedicated entrance for breast center patients, imaging services (MRI, CT, Ultrasound, X-ray. PET, Mammography, Bone Densitometer), Infusion Center, and Radiation Oncology Services.
Mechanical systems include the following:
- Aluminum MRI Quench Vent
- (3) AHU’s
- (2) Air Cooled Chillers, (2) Medical Equipment Chillers, (1) Linac Chiller
- (3) Hot Water Boilers
- (18) CRAC Units
- (7) CHW, HHW, and FPP pumps
- (1) Glycol Pump System
- Storage Tank, Expansion Tanks, and Air Separators
- (8) Cabinet Unit Heaters
- (31) Baseboard Fin Tube Radiators
- (96) Supply Terminals
- (4) Duct Mounted Reheat Coils
- (2) Gas Humidifiers, (1) Electric Humidifier
- (5) Exhaust Fans
- (9) Fan Filter Units
- (1) Filter Housing
- (22) Fire Smoke Dampers
- (13) Electric Radiant Heat Panels
- Pneumatic Tube HDPE Conduit System
Key Project Elements:
- 100% Revit MEP Prefabrication
- Coordination
- Total Station Hanger and System Layout
- Multi Location Prefabrication – On Time delivery
- Duct: Supply, Return, Exhaust, Hazardous Exhaust, Grease Duct, Isolation Duct, Pharmacy Duct, Fume Hoods, VAV’s & Air Valves, Underground Ductwork
- Mechanical Piping: HHW, CHW, Gas, Refrigerant Piping, Cooling Tower Water, Radiant Panels
- Medical Gas: CA
- AHU’s, Cooling Towers, Chillers, Boilers, Pumps, Split Systems, CRAC Units, Humidifiers, Linac Chiller, Medical Equipment Chillers, and Radiant Panels
- MRI, Linear Accelerator, Radixal Vault, CT, X-Ray, and Pharmacy
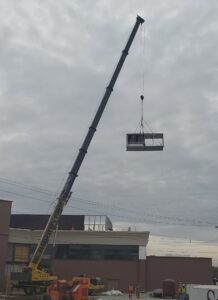
This design-assist project complies to LEED Credit EQc4 requirements. We performed extensive amounts of multi-trade prefabrication on this project. The fit-out of the third-floor shell space was added to our scope after the project started. Since the building was already enclosed, this required an on-site paint booth and multi-trade rack fabrication in the shell space.
The multi-trade racks are located throughout the project in every corridor. Since there are no ceilings in the corridors, this was our first exposed installation of our multi-trade prefabrication.
Our scope is for the Mechanical Ductwork and Piping for the building including the following:
- (2) Custom AHU’s totaling 30,000 CFM
- (123) Chilled Beams
- (56) 6-Way Control Valves
- Fit Out of Third Floor Shell Space
- On site Multi-Trade Rack Fabrication and Paint Booth
- (68) VAV Terminals
Key Project Elements:
- 100% Revit MEP Prefabrication
- Design-Assist
- Coordination
- Total Station Hanger and System Layout
- Multi-Trade Racks – Architectural Features, Mechanical Pipe, Duct, Plumbing, Lighting, Electric and Fire Protection
- Mechanical Site Piping: Campus Loop Tie-ins and Manholes
- Mechanical Piping: HHW, CHW, Chilled Beams, 6-way Valves, Refrigerant
- Ductwork: Supply, Return, Exhaust, VAV’s & Chilled Beams
- Lower-Level Mechanical Room
- Penthouse

This project was a gut renovation of the existing 4-story 83,000 Square Foot building. It included approximately 10,000 square feet of Vivarium, and the rest of the building is split about 50/50 between Research and Teaching Laboratories. Our scope is for the Mechanical Ductwork, Piping, Plumbing and Lab gas services for the building including the following:
- Two custom AHU’s totaling 75,000 CFM
- Lab Exhaust system – 40,000 CFM
- Piped Lab utilities included Oxygen, Carbon Dioxide, Vacuum, Nitrogen, Compressed Air, and Natural Gas
- New Lab Vacuum, Lab Air, and Lab Reverse Osmosis Water Systems.
- 68 VAV Terminals and 40 Phoenix Supply Air Valves
- 10 VAV Exhaust Air Valves and 32 Phoenix Exhaust Air Valves
Key Project Elements:
- Design-Assist
- Research Lab
- Duct: Supply, Return, Exhaust, Hazardous Exhaust, Fume Hoods, VAV’s & Air Valves
- Lab Gas: RO, CO2, O2, VAC, CA, N2
- Mechanical Piping: HHW, CHW, G
- AHU’s, Pumps, Split Systems, Vivarium Exhaust Fans, Side Wall Exhaust Fans, Laboratory Exhaust Fans, Air Valves, Electric Air Curtains, RO Skid, Vacuum Pumps, Lab Air Compressor and Lab Gas Manifolds
This project consisted of a four-story addition of approximately 78,000 gross square feet to the existing UMSL Benton Hall Science Complex. RHMC provided the Mechanical Ductwork, Piping and Lab gas services for the building including the following:
- (2) Custom AHU’s totaling 75,000 CFM
- Lab Exhaust system with Energy Recovery Coils – 38,500 CFM
- New Central Chilled Water Plant for the entire Science Complex – initial capacity of 1,300 tons with ultimate capacity of 2,600 tons
- New Central Heating Plant for the entire Science Complex – initial capacity of 12,000 MBH with ultimate capacity of 36,000 MBH
- New Central Laboratory Vacuum, Laboratory Air, and Reverse Osmosis Systems
- Piped Lab Utilities included Vacuum, Compressed Air, Natural Gas, Reverse Osmosis
- (43) VAV Terminals and (35) Phoenix Supply Air Valves
- (21) VAV Exhaust Terminals and (95) Phoenix Exhaust Air Valves
Key Project Elements:
- 100% AutoCAD MEP Prefabrication
- Coordination
- Total Station Hanger and System Layout
- Duct: Supply, Return, Exhaust, Stainless Steel Welded Hazardous Exhaust, Fume Hoods, VAV’s, & Air Valves.
- Mechanical Piping: HHW, CHW, Refrigerant, Gas
- Lab Gas: LA, LVAC, DI, N2
- Piping Racks – Lab and Mechanical Piping
- Penthouse and Basement Mechanical Plant
- Energy Recovery and Future Planning
- RO Piping and Specialties, Cooling Tower, Chillers, Custom AHU’s, Duct Mounted Coils, Supply, Exhaust and Fume Valves, Tracking Boxes, Duct Silencers, Custom Fume Hoods, Lab Gas Zoning Valves and Specialties, Boilers, Fin Tubes
This project consisted of a new 260,000 square foot Replacement Hospital and a new 100,000 square foot Medical Office Building.
A Design-Assist project, our BIM Department was brought on with the KJWW team at Schematic Design, the rest of our construction team was brought on after Design Development. After Design Development was issued, all modeling was completed by Rock Hill Mechanical. We were also the BIM Lead and managed the BIM coordination process and clash detection and resolution.
Key Project Elements:
- 100% Revit Prefabrication
- Coordination
- Total Station Hanger and System layout
- Multi Location Prefabrication – On Time delivery
- Duct: Supply, Return, Exhaust, Hazardous Exhaust, Grease Duct, Isolation Duct, Pharmacy Duct, Fume Hoods VAV & Air Valves, Black Iron, Galvanized, Stainless Steel and Aluminum Ductwork
- Mechanical Piping: HHW, CHW, Gas, Cooling Tower Water, Steam, Fuel Oil, Condensate and Condenser Piping
- Medical Gas: O2, NCW, DI, CO2, VAC, N, MA, CA, N2O, WAGD, RO
- Prefabrication: Headwalls, Zone Valve Boxes, Flat Piping Racks
- Multi-Trade Racks – Mechanical Pipe, Med Gas, Duct, Patient Lifts, Electrical, Minimal Plumbing
- (14)OR’s, (2) IR’s, (4)ICU’s, CT, MRI, Xray, Pharmacy, and ER
- AHU, Roof Top Units, Fan Coils, Blower Coils, Chillers, Energy Recovery, Cooling Towers, Boilers, Pumps, Humidifiers, Exhaust Fans, Relief Fans, Kitchen Exhaust Fans, Dishwasher Exhaust Fan, Elevator Exhaust Fan, Heat Exchangers, VAV, Tracking Boxes, Return VAV boxes, Air Valves, Instrument Air Compressors, Medical Air Compressors, Vacuum Pumps, Medical Gas Manifolds, Master and Area Alarm Panels, Medical Zone Valve Boxes, and Med Gas Outlets
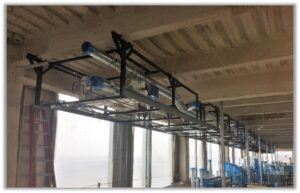
This was a new building with 90,000 Square Feet of primarily Laboratory Space. The project had a requirement of obtaining LEED Silver. Rock Hill played an integral part in meeting this goal by the implementing of an efficient design, running an energy model, and by carrying out the LEED required documentation prosses. Rock Hill led the MEP virtual pre-construction coordination prosses. The extensive coordination prosses allowed the team to prefabricate a large amount of buildings MEP systems with great success. Rock Hill also facilitated, built, and installed multi-trade racks in the corridors of the two lab floors resulting in a cleaner installation, and a shortened construction schedule. Our scope was for the Mechanical Ductwork, Piping, and Lab gas services for the building including the following:
- (1) Custom AHU-Totaling 85,000 CFM
- Lab Exhaust System – 65,000 CFM
- Piped Lab Utilities including Oxygen, Carbon Dioxide, Vacuum, Nitrogen, Compressed Air, and Natural Gas
- New Lab Vacuum, Lab Air, and Lab Reverse Osmosis Water Systems
- New 2400-ton Central Chilled Water Plant for Science Complex
- New 9000 MBH Boiler Plant
- (64) VAV Terminals and (25) Phoenix Supply Air Valves
- (88) Phoenix Exhaust Air Valves
Key Project Elements:
- 100% Revit Prefabrication
- Total Station Hanger and System layout
- Coordination
- Duct: Supply, Return, Exhaust, Stainless Steel Welded Hazardous Exhaust, Fume Hoods, VAV, & Air Valves
- Mechanical Piping: HHW, CHW, Refrigerant, Gas
- Lab Gas: LA, LVAC, DI, N
- Multi-Trade Racks – Mechanical Pipe, Lab Gas, Duct, Fire Protection, Electrical, & Plumbing
- Penthouse and Basement Mechanical Plant
- Energy Recovery and Future Planning
AHUs, Cooling Towers, Chillers, Boilers, Pumps, Split Systems, Strobic Lab Exhaust Fans, Hot Water Unit Heaters, Air Valves, Electric Air Curtains, RO Skid, Vacuum Pumps, Lab Air Compressor, and Lab Gas Manifolds
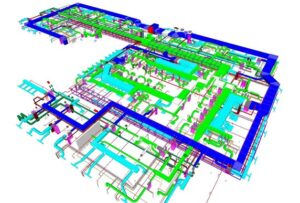
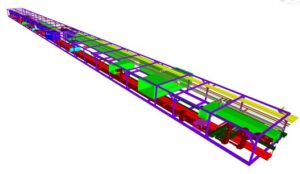
This project consisted of a new 328,000 square foot Hospital including:
- (134) Private Patient Rooms in the following nursing units
– Cardiac
– Orthopedics/Neurology and Rehabilitation
– Surgical and Oncology
– Medical and Pulmonary
– Intensive Care Unit
- 20-room Emergency Department
- Surgery Department including 6 Operating Rooms
- Imaging, including 2 CT Scanners and 1 MRI
- Women’s Center
- Rehabilitation Center
This project was one of the first full BIM projects completed in the Midwest by any construction team and Rock Hill was the Mechanical Contractor.
Key Project Elements:
- 100% AutoCAD MEP Prefabrication
- Coordination
- Dimension Based Hanger and System layout
- Multi Location Prefabrication – On Time delivery
- Duct: Supply, Return, Exhaust, Hazardous Exhaust, Grease Duct, Isolation Duct, Pharmacy Duct, Fume Hoods VAV & Air Valves, Black Iron, Galvanized, Stainless Steel and Aluminum Ductwork.
- Mechanical Piping: HHW, CHW, Gas, Cooling Tower Water, Steam, Fuel Oil, Condensate and Condenser Piping
- Plumbing: Storm, Sanitary, Domestic Water, and Specialties
- Medical Gas: O2, NCW, DI, CO2, VAC, N, MA, CA, N2O, WAGD, RO
- Prefabrication: Headwalls, Zone Valve Boxes, Flat Piping Racks
- (6) OR’s, (134) Patient Rooms, ICU’s, CT, MRI, Xray, Pharmacy, and ER
- AHU, Roof Top Units, Fan Coil Units, Blower Coils, Chillers, Energy Recovery, Cooling Towers, Boilers, Pumps, Humidifiers, Exhaust Fans, Relief Fans, Kitchen Exhaust Fans, Dishwasher Exhaust Fan, Elevator Exhaust Fan, Heat Exchangers, VAV’s, Tracking Boxes, Return VAV boxes, Air Valves, Instrument Air Compressors, Medical Air Compressors, Vacuum Pumps, Medical Gas Manifolds, Master and Area Alarm Panels, Medical Zone Valve Boxes and Med Gas Outlets, Fuel Oil Tank
This project consisted of a new 130,000 square foot patient tower located on the main campus. A new main entrance to the hospital was also incorporated into this addition.
This addition has stand‐alone Mechanical systems including the following:
- (4) Custom Air Handling Units – Total CFM 140,000
- (2) 400‐ton Air-Cooled Chillers
- (3) 168 Horsepower Condensing Dual Fuel Boilers
- (212) Variable Air Volume Terminal Units with Hot Water Coils
- (1) 10,000-Gallon Underground Fuel Oil Tank
- New Medical Air, Vacuum, and Bulk Oxygen systems
RHMC was brought in at the inception of the project on a design-assist basis to work with the project team. We worked with the electrical subcontractor to develop multi‐trade patient room racks that house the reheat, medical gasses, and power conduits. We also prefabricated all of the headwall services together in a similar fashion.
Key Project Elements:
- Design-Assist
- Total Station Hanger and System layout
- Coordination
- 100% Revit Prefabrication
- Duct: Supply, Return, Exhaust, Grease Duct, Isolation Duct, Fume Hoods, VAV & Air Valves, Underground Duct
- Mechanical Piping: HHW, CHW, Ref, G, Fuel Oil, Steam, Underground Natural Gas and Fuel Oil
- Medical Gas: MG,MA;O2,Vac, Underground O2
- Prefabrication: Headwalls, Zone Valve Boxes, Flat Piping Racks
- Multi-Trade Patient Room Racks
- Air Handling Units, Roof Top Air Handlers, Air-Cooled Chillers, Pumps, Exhaust Fans, Humidifiers, VAV with Reheat Coils, VAV with Electrical Reheat, Air Curtains, Fan Terminal Units, Boilers, Medical Gas Zone Valve Boxes and Outlets, Medical Area Alarms, Vacuum Pumps, Medical Air Compressors, and Medical Gas Manifolds
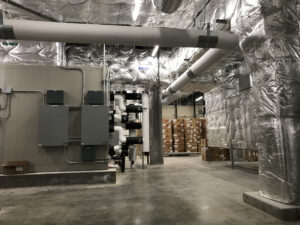
This project consists of a new 750,000 square foot tower located at the corner of Forest Park Avenue and Kingshighway. We performed the work on the fit‐out of the entire building including the following:
- 23,000 square foot Kitchen and Dining area
- 2200 square foot Auditorium
- 41,000 square foot Central Sterile Processing Department
- (9) Conventional Operating Rooms
- (3) Robotic Operating Rooms
- (5) Interventional Radiology Rooms
- (2) C‐Section Operating Rooms
- (1) Infant Operating Room
- 40-bed Post Anesthesia Care Unit
- (37) LDRP Rooms
- (35) Conventional Patient Rooms
- (15) Medical Surgical Intensive Care Rooms
- (10) Bone Marrow Transplant Intensive Care Rooms
- (160) Bone Marrow Transplant Patient Rooms
To meet the project schedule, we fully modeled the project and prefabricated the following items in our shops:
- (109) Patient Room Multi‐Trade Racks
- (153) Mechanical piping racks
- (297) Medical Gas Headwalls
- (729) Supply terminal box reheat trims
Key Project Elements:
- 100% Coordination & Prefabrication, 75% Revit Prefabrication remaining Cad MEP
- Coordination
- Total Station Hanger and System Layout
- Multi Location Prefabrication – On Time Delivery
- Duct: Supply, Return, Exhaust, Hazardous Exhaust, Grease Duct, Isolation Duct, Pharmacy Duct, Fume Hoods, VAV & Air Valves.
- Mechanical Piping: HHW, CHW, Gas, Cooling Tower Water, Kitchen Filtered Water, Kitchen Oil Conduit, Steam Piping, Condensate, Kitchen Indirect Waste Piping, PEX Tubing for Radiant floor
- Medical Gas: O2, NCW, DI, CO2, VAC, N, MA, CA, N2O, WAGD, RO
- Prefabrication: Headwalls, Zone Valve Boxes, Flat Piping Racks
- Multi-Trade Racks – Mechanical Pipe, Med Gas, Duct, Patient Lifts, Minimal Electrical & Plumbing.
- Exhaust Fans, Relief Fans, Kitchen Exhaust Fans, Dishwasher Exhaust Fan, Exhaust Fan, Heat Exchangers, VAV, Tracking Boxes, Return VAV boxes, Air Valves, Instrument Air Compressors, Medical Air Compressors, Vacuum Pumps, Medical Gas Manifolds, Master and Area Alarm Panels, Medical Zone Valve Boxes and Med Gas Outlets
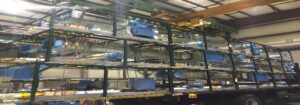